
Volker Shultz, Essar Oil UK chief executive
Essar Oil UK has reconfigured its Stanlow Refinery to increase the production of high value products and further reduce the amount of fuel oil and naphtha produced on the site.
Maintenance has recently been completed on a key furnace in the main distiller unit, and the site’s smaller CD3 crude distillation unit has been mothballed earlier than originally planned, resulting in reduced fuel oil and naphtha production, and improved margins and cost efficiencies.
It is expected that Stanlow’s yield profile will be approximately 33% gasoline, 57% kerosene and diesel and 3% fuel oil, with crude and feedstock throughput reducing from 75 to 71 million barrels per annum.
This is the latest in a series of cost efficiency initiatives at Stanlow, which include the expansion of the refinery’s crude slate, the 25 year “re-lifing” of Europe’s largest catalytic cracker, and the introduction of natural gas fuel to all high pressure boilers on site.
In addition, the recent voluntary leaver incentive scheme, proposed by a joint working group of employees, has been well received by staff, with organisational changes already delivering additional cost savings.
Essar Oil UK chief executive, Volker Schultz, commented: “This new optimised configuration has delivered an immediate improvement to our refining economics. This is in addition to the margin enhancement initiatives already introduced, with a large number of other projects still ongoing.
“Despite the challenges facing the European refining industry, Stanlow is becoming an even more advantaged site, having undergone a major turnaround only last November, including the 25 year re-lifing of Europe’s biggest cat cracker.
“The entire business is committed to identifying and implementing additional opportunities to improve margins, with organisational streamlining also strengthening our competitive position and ensuring we have the right blend of skills and experience to build a positive and long term future for our business.”
Stanlow produces approximately 15% of UK transport fuels, including three billion litres of petrol, 3.5 billion litres of diesel and two billion litres of jet fuel per year.
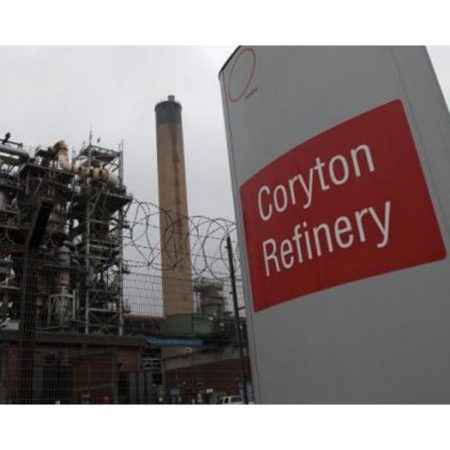
Thames Enterprise Park has taken a major step towards the economic development of the site of the former Coryton Refinery with the appointment of contractors to demolish the redundant refinery and boiler house.
A vision prepared by the owners of Thames Enterprise Park for creation of a centre of excellence in energy and environmental technologies has won the support of Thurrock Council. Up to 400 acres of the 580-acre former refinery site are to be used for Thames Enterprise Park, with 140 acres now immediately available and another 70 acres to be freed up by the clearance of the refinery.
The former refinery’s tanks, jetties and loading racks are being converted into a deep water import and blending terminal at neighbouring Thames Oilport, the design of which is still under review, so will not be demolished by the contractors.
Graham Alexander, head of business development at Thames Enterprise Park, commented: “The business of Thames Enterprise Park is progressing well ahead of our investment expectations. The potential of the site has become very obvious since we took ownership. It is a great strategic location for business and, as an established industrial site with river, road and pipeline access, has a unique set of attributes.”
Cllr John Kent, leader of Thurrock Council, said: “While it’s sad to see another of Thurrock’s old landmarks disappear, at the same time it’s exciting as another dynamic industry rises here and utilises our unique geographical advantages.”
Demolition of the refinery is expected to take approximately two years.
For more about the Coryton refinery – see also page 7 in the October 2014 issue of Fuel Oil News
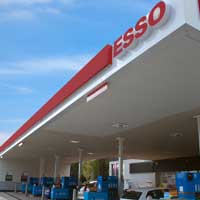
Greenergy now supplies Esso dealerships nationally
Greenergy has begun supplying Esso fuel to Esso branded independent dealerships in the Midlands, the South of England and South Wales.
Greenergy has been a branded wholesaler for Esso since February 2013 when it took over fuel supply to Esso branded dealerships in the north of England, north Wales and Scotland. The agreement now extends nationally with Greenergy taking over supply to a further 104 Esso branded dealerships.
Greenergy also has rights to market the Esso brand to independent forecourts nationally, offering Esso-branded fuel alongside its other brand options. Both the number of Esso branded sites supplied by Greenergy and their sales volume have grown strongly under the branded wholesaler arrangement.
Andrew Owens, Greenergy chief executive said: “There has been considerable interest from dealers looking for a major oil brand and loyalty scheme with Greenergy’s flexible terms, competitive pricing, supply reliability and customer responsiveness. This is a unique combination, making it one of the strongest fuel offerings in the UK.”
Duncan Connolly, retail director of Esso Petroleum Company Limited commented: “Greenergy already supplies high quality Esso fuels to independent dealers in the northern half of the country and has attracted 25 additional independent dealer sites to switch to the Esso brand.”
Meanwhile, Shailesh Parekh of Midland Link service station, for whom fuel supply has now transferred to Greenergy, said: “I’m excited that Greenergy is now my supplier of Esso fuel. I’ve heard great things about their flexibility, efficiency and hands-on approach to customer service.”
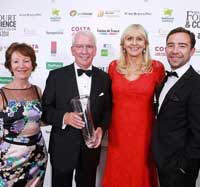
Left to right: Tom Noonan’s wife Mary, Tom Noonan, compere Miriam O’Callaghan and Tom Noonan junior
Maxol chief executive officer, Tom Noonan, was presented with the inaugural Lifetime Achievement Award at Ireland’s ninth annual Forecourt & Convenience Retailer (IFCR) awards ceremony in Dublin earlier this month.
Tom, who joined Maxol 35 years ago as a personnel manager, accepted the accolade from the awards’ host, Irish radio and television presenter, Miriam O’Callaghan.
He told the 350-strong audience that he was delighted to win the award and spoke about his time working in the Irish fuel industry, the people he has encountered over the years and how Maxol’s forecourt and convenience business has continued to develop during his tenure.
Tom added that when he joined Maxol, the industry was 90% owned by foreign firms but that today it is 75% owned by Irish companies who are setting the standard in forecourt convenience retailing that is the envy of similar operations around the world. “Maxol is at the forefront of this movement, as evidenced by the recent launch of our new food brand “Moreish”, which highlights our dedication to further evolving and enhancing Maxol’s overall forecourt experience.”
Maxol also had another winner on the night as Conway’s Maxol/Spar, Ratoath, Co Meath picked up the award for the “Best Site” with a licence to sell alcohol.
Bill Penton, publisher of IFCR and organiser of the awards event, said that he had been very impressed by the high calibre of all the finalists in this year’s competition.
“Continuous investment in new forecourts means that the standards are getting higher every year and that means much-needed new jobs and support for Irish suppliers, growers and manufacturers,” he said.
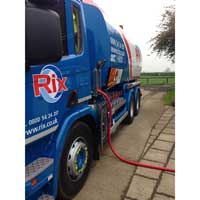
One of the 17 new trucks operated by Rix Petroleum, featuring the new TE550 Truck 111 system from Alpeco
Alpeco Limited, a company within the Flomax Group, has won its largest order to date for their new TE550 Truck III electronic register system from Hull-based Rix Petroleum.
Rix Petroleum appointed Alpeco as the preferred equipment supplier for 17 new trucks ordered in June 2013 from Tasca Tankers. 90% of the Rix Petroleum fleet are already fitted with Alpeco products and Alpeco and Liquid Controls tailored the development of the new TE550 Truck III to provide Rix with a bespoke electronic register system.
All 17 tankers are now in service and two of them have operated the TE550 Truck III electronic register successfully since their introduction. The remaining 15 trucks will now be upgraded with the new system which has been designed specifically to address the growing need for operators to monitor the volumes of fuel loaded, delivered and left on board the tanker at any given time.
The system’s inventory software allows the operator to input the volumes and grades of product loaded into each vehicle compartment. Once this information has been entered and saved, an in-cab printer produces a bill of laden confirming the time, date and the load details. As the tanker completes each delivery the volume discharged is then automatically deducted from the respective inventory and the volume left on board is shown on the meter display.www.alpeco.co.ukhttp://rix.co.uk
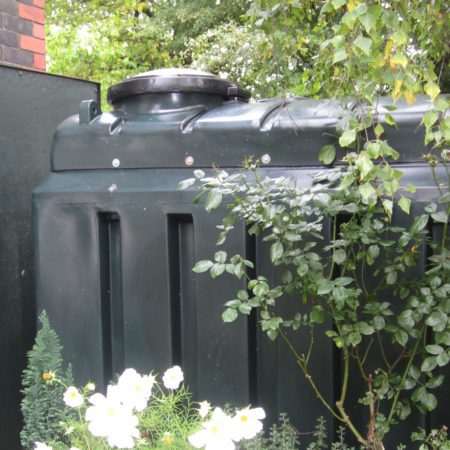
Heating oil consumers across the UK are being urged to change their energy habits and order heating oil early before the winter weather arrives.
The FPS (Federation of Petroleum Suppliers) has joined forces with the government and consumer bodies ACRE (Action with Communities in Rural England), Citizens Advice Bureau and Consumer Futures, to launch its “buy oil early” campaign – a move which has the support of energy minister, Matt Hancock, who commented: “The nights are drawing in and winter is just around the corner, so we are encouraging people to stock up on oil sooner not later.
“It’s better to order early when demand is low and prices are low and to make sure no household is caught out, especially in remote and rural areas where roads can be disrupted and delivery times only increase as the weather gets worse.”
Chief executive of the FPS, Mark Askew, comments: “We have launched a ‘buy oil early’ campaign now in association with the government and consumer agencies and we hope people will heed our combined advice. We are urging people not to leave it to the last minute when the bad weather has taken hold and tanker drivers struggle to get through on roads covered in snow or ice. In addition, compared to how much it cost the 1.5 million off-grid energy users to heat their homes using oil last year, it’s now a lot cheaper – which is obviously great news for households who use oil.”
The FPS is advising customers to set up a regularly monthly payment with their local oil supplier in order to offset higher bills during the winter months.
“In an economic climate where energy prices are in the news daily, we are trying to educate consumers on ordering early and therefore pay less and manage their fuel budget better throughout the year,” adds Mark Askew.
The FPS has also posted a list of money-saving tips and advice on managing energy needs on their website www.oilsave.org.uk
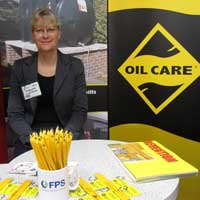
The Oil Care Campaign will be celebrating its 20th anniversary at its conference and exhibition on 4th June 2015 at the National Motorcycle Museum near Birmingham.
The campaign was set up by the Environment Agency in association with the Scottish Environment Protection Agency (SEPA) and the Northern Ireland Environment Agency (NIEA), to reduce oil pollution by providing guidance on the safe disposal and management of oil. A network of oil banks which accept used engine oil for recycling has been established in England, Wales, Scotland and Northern Ireland.
Organisers of next June’s event are offering the opportunity to support the campaign for £250. This will include a table in the exhibition room and entry for two people to the conference itself.
Since it was launched in 1995, the Oil Care Campaign has helped reduce oil pollution incidents across England and Wales from nearly 7,000 a year to under 2,600 in 2013. In the 12 months to April 2014 more than 37,500 people used the oil bank website to find the location of their nearest oil recycling facility.
Event and exhibition booking information is available from Oil Care Campaign manager, Liz Hobday at: liz.hobday@environment-agency.gov.uk

Suttons Group has acquired Imperial Tankers, one of the largest bulk chemical transport companies in the UK, from Hargreaves Services PLC. Terms of the transaction have not been disclosed.
Established in 1989, Imperial Tankers has a road tanker fleet of over 200 tractor units and 350 tanker semi-trailers and provides both fully-managed logistics solutions and single spot product movements to deliver a wide range of hazardous and non-hazardous chemicals and other sensitive products.
John Sutton, Suttons Group CEO, said: “This transaction is an ideal fit for Suttons and will enable us to continue to deliver high levels of safety and service, improve efficiency and add value through supply chain resilience and innovation. Our joint depot network will enhance our ability to provide an outstanding service to customers in key production regions around the country.
“Our combined fleet of over 700 road tankers gives us an even greater ability to support our customers through times of peak demand and react rapidly to changing customer requirements.”
This is Suttons’ third acquisition in the last 12 months. In October 2013 the company completed the purchase of Chinese transport company Hanchi Logistics, and in August 2014 the company acquired IS Logistics Group, a logistics and supply chain specialist based in Singapore. The acquisition of Imperial Tankers reflects Suttons’ commitment to growth in the bulk logistics and supply chain sector.
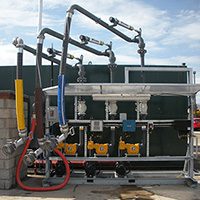
IFC Inflow will be among the exhibitors at this month’s Tank Storage Association exhibition and conference which takes place at the Ricoh Arena on Thursday 18th September.
A leading supplier of tanker loading equipment and tanker safe access systems, the company offers a range of equipment including petroleum & chemical loading arms, tanker loading skids, loading platforms and gantries, self-levelling folding stairs, mobile safe tanker access equipment and high speed bulk loading systems.
Petroleum bottom loading arms – The 445 series arm is designed for heavy duty use at petroleum terminals and distribution depots. It is the ideal replacement for first generation arms reaching the end of their life and for new applications requiring high performance at a low cost.
Chemical loading arms – Articulated top and bottom loading arms for chemical and food applications. Custom designed and tailor made for individual customer requirements. Typically made from carbon or stainless steel, options include pneumatic control, overfill sensors, vapour cones, lagging and trace heating and PTFE lining for very aggressive applications.
Petroleum loading skids – Factory built & tested loading skids are ideal for terminal applications where flexibility and speed are essential. Offering flow rates up to 2500 l/min, high accuracy metering, up to 6 product arms per system, fully compliant with ATEX regulations. Optional blending and additive injection control systems.
Safe tanker access – Gantries and platforms designed to comply with the latest work at height regulations and when fitted with our self-levelling folding stairs provide the safest way for operators to access the tops of tankers.
Folding stairs – Providing safe access to any height tanker, stairs come in a range of sizes and when fitted with an optional safety cage offer total operator safety while working on the tops of tankers. Options include pneumatic control, cages in special sizes and materials, press down facility and cage infill grating.
A major event, potentially affecting tens of thousands of people and some of the biggest employers in the country, happens in Scotland this week. Yes, you guessed it – The Scottish Energy Careers Festival 2014!
On Wednesday, September 17th – just 24 hours before that other Scottish event – at Glasgow’s newest conference and event venue, 200 St. Vincent Street, some of the most influential employers in Scotland’s flourishing oil and gas sectors will be meeting ambitious professionals with skills and qualifications that are in high demand in the country’s energy sector.
Although direct employment with some of the big names in Scottish energy, may be relatively small, the number of jobs which depend on the sector is huge.
David East, communications manager for the INEOS facility at Grangemouth, says that around 1400 people are directly employed at the site, plus contractors employed by third party companies. However, “Scottish Key Facts”, released by Scottish Enterprise in May this year, estimated that more than 13,500 jobs were directly associated with the country’s chemicals industry with another 70,000 people whose jobs depended on the sector.
The Scottish Energy Careers Festival, organised by s1jobs, takes place on Wednesday 17th September between 11am and 8pm at 200 St. Vincent Street, Glasgow.
www.s1jobs.com/newsandguides/the-scottish-energy-careers-festival-2014.html