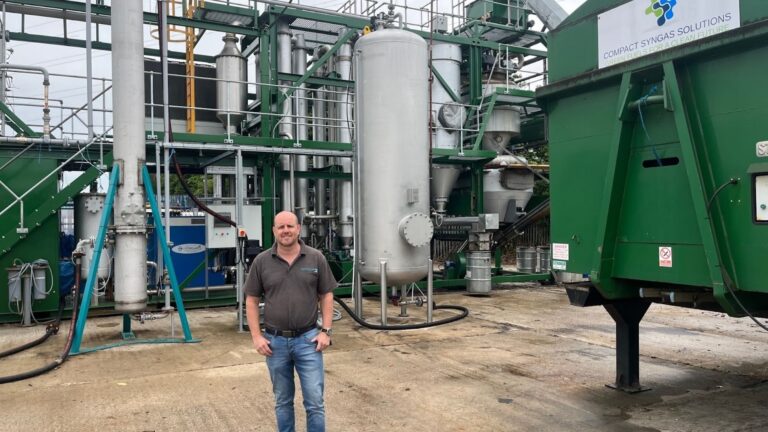
Separating hydrogen from syngas
CSS designed and built its own Pressure Swing Absorption (PSA) system to separate hydrogen from syngas instead of relying on expensive third-party suppliers to the petrochemical sector.
The design is expected to evolve into a two-stage PSA process, with the intention of meeting the requirements of the waste-to-energy sector by keeping the operating pressure in the region of 3 barg (pressure in bars above atmospheric pressure) and to reach greater than 98% purity.
Waste-to-energy processes rely on an advanced gasifier that turns waste into raw syngas and char, which is the first, hugely important step in the carbon capture process.
The syngas is a gas mixture containing hydrogen, carbon monoxide, carbon dioxide, methane, nitrogen, water vapour and bio-oils and trace contaminants. The bio-oils, water vapour and trace contaminants need to be removed to create a clean syngas.
After a number of gas clean-up stages PSA was used in two stages. CSS built and demonstrated this process on a real syngas to be capable of producing greater than 95% purity hydrogen gas.
In these preliminary plant trials, the PSA process was demonstrated to work at even low operating pressures (1.5 barg), and with just a two-stage PSA process. Further work is now planned at higher operating pressures to understand the balance between capital and operating costs in this particular waste-to-energy business setting and its scale of operation.
Government funding
CSS recently secured almost £4 million in government funding to make its biomass and waste-to-hydrogen plants even greener by using carbon capture.
The company has a vision of building more than 50 hydrogen modules at around 15 sites, ranging from a single module to six per site offering the flexibility to suit local demand, providing hydrogen and electricity.
These 50 modules in total could:
- Produce 3,000 tonnes a year of hydrogen
- Generate 12.4 MW of electricity powering the technology, and
- Capture 150,000 tonnes per year of equivalent carbon dioxide in the char.
They also have the potential to capture another 38,000 tonnes a year of carbon dioxide from the syngas produced.
Overcoming the technical challenges
Professor Stan Kolaczkowski, chief technical officer at CSS, said:“The conversion of a waste material into a gas from which hydrogen can be separated is not an easy process, and there are many technical challenges to be overcome.
“The presence of bio-oils and trace levels of contaminants in the syngas and their impact on down-stream processing cannot be ignored. Developers need to proceed with caution and scale-up their processes carefully.
“Investors are too often in a rush to build a large plant, and do not get advice from chemical engineers with know-how in this specialist field.
“The conversion of waste into a gas which can be used as an energy vector is much better for the environment, rather than allowing the waste to degrade in a landfill or be sent to an incinerator.
“The know-how we have gained on PSA techniques could be of value to other companies who have an interest in this sector. We are willing to explore collaboration in this field and also starting to explore carbon dioxide capture using PSA techniques.
Paul Willacy, CSS’ managing director aded:“Using pressure swing adsorption to separate hydrogen from a syngas derived is well-known, but we struggled to find equipment suppliers who would work with us on smaller R&D trials.
“As a result of this, we decided to develop our own PSA scheme for our plant trials, which we did at a low cost. We proved the technique at low pressures using real syngas generated from waste. This was a real trial and not just an academic exercise.
“Many small companies are leading the innovation powering us towards a greener hydrogen-powered future, and this inventive process is one example of how we’re getting it done.”