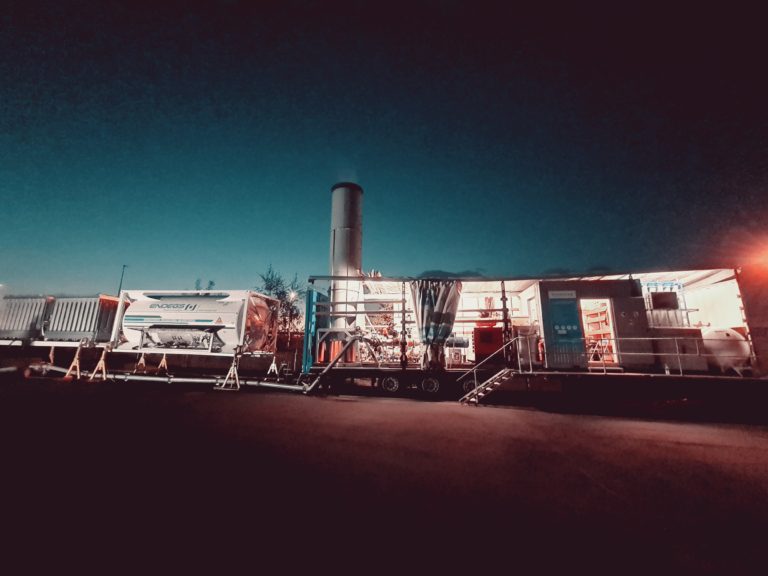
Emission control
With a keen eye on net zero, mobile degassing specialist, ENDEGS is helping depots and tank terminals to actively reduce and treat emissions.
The company’s solution solves the illegal, and potentially hazardous, venting of hydrocarbon emissions into the atmosphere. It was developed as a response to the 2010 Industrial Emission Directive in a bid to help oil and gas companies become legally compliant.
“The service we deliver is compliant with environmental legislation, increases safety, lowers risk in operation and does not impact on neighbouring residents with noise, odour or visible flame,” comments managing director, David Wendel.
ENDEGS’ degassing solution also offers additional advantages as David illustrates: “Imagine that the vapour recovery system at a tank terminal malfunctions and the owner is tasked with finding a replacement solution or has to stop loading activity altogether, it could prove financially disastrous. In this situation, using the ENDEGS solution could deliver financial benefits.”
In the ever-changing world of liquid fuels, ENDEGS is flexible and keen to move with the times as David points out: “We’re driven to evolve with our clients and create and deliver innovation. We take any client requests seriously.” Good news for distributors looking to move into biofuels.
Proving this point, ENDEGS has been named one of the 100 most innovative companies in Germany for two years in a row. Although its solution was originally aimed at oil and gas products, it has since upgraded its technology and has carried out projects with new fuels such as hydrogen and biofuels, which bodes well for the sector moving forward.
In addition to its emission reduction services, the company also rents out ATEX zone 0 robots for no-man entry tank cleaning, carries out nitrogen services with its own fleet of mobile atmospheric vaporisers and hires out specialist equipment such as mobile detonators, flame arrestors, pipings, power generators and pressure reducers.
On a roll
Depots are always going to need concrete for hard engineering applications such as bund linings, containment, erosion control, scour protection and weed suppression, but Concrete Canvas goes one step further.
Part of a revolutionary new class of construction materials called Geosynthetic Cementitious Composite Mats (GCCMs) designed to replace conventional concrete in erosion control applications, Concrete Canvas is a flexible, concrete-filled, geotextile that hardens on hydration to form a thin, durable and waterproof concrete layer.
Originally developed in 2004 as part of a university project for the rapid deployment of concrete humanitarian shelters, the company moved into the civil sector in 2009 and now works widely in the petrochemical industry.
“The material has a BBA durability of 120 years for erosion control solutions,” says Blake Williamson, the company’s technical sales representative South East (UK). “It’s faster and easier to install than standard concreting methods and offers a lower carbon solution. Essentially, it’s concrete on a roll.”
Concrete Canvas and its sister product, CC Hydro (CCH) can be installed with minimal, or no, plant requirement and there’s no risk of back- spray, debris or rebound, thus protecting sensitive infrastructure at depots. The materials are quicker to install than traditional alternatives, reducing time on site and asset downtime – elements that are vital for depots.
CCH is a revolutionary containment product which combines the company’s concrete-filled, geotextile technology with a highly impermeable, chemically resistant, geomembrane backing. The geomembrane provides a high-performance liner with a testable joint for quality assured containment applications, essential for fuel depots. The liner incorporates a hi-visibility welding strip allowing joints to be thermally bonded with a twin-track or triple-track air channel for on-site testing.
It also provides effective weed suppression, eliminating the ongoing maintenance cost of soil-covered systems.
“Incredibly durable, it has a hard armour surface, protecting the geomembrane liner from puncture, abrasion, weathering, burrowing animals and UV degradation,” adds Blake.
The product is proving a big hit in the energy sector, as Blake explains: “Although we only began commercial volume production of CCH in 2015, we now supply seven out of the top 10 oil and gas operators worldwide.”
Valve solutions
Fuel depots require a considerable number of valves and finding a trusted supplier is a major consideration.
AC Valve Alliance Group is a specialist distributor of valves, which have been manufactured in exotic materials for chemical compatibility. The company holds an enormous range of stock from major valve and automation manufacturers, such as Perar and Starline, Pekos, Air Torque, Galli & Cassina, Nacional Safety Valves, Zwick and Sammi – brands that are all used extensively in oil and fuel storage applications due to their superior design, material and construction suitability.
The majority of the company’s products are manufactured in Western Europe and have approval from some of the world’s biggest oil companies, such as Total, Shell and Aramco. Developed with a range of resilient materials for seat and seals, to cover all types of fuels and chemicals, they are ideal for use in fuel depots. The Pekos tank bottom valve range in particular, has been specifically designed for allowing an actuated quarter-turn ball valve to be fitted at the bottom of storage vessels.
The company has extensive depot experience, as technical manager, Nick Papworth explains: “We have supplied products for use in depots throughout our 25 years in business and have always received positive feedback. Our team of experts have a huge wealth of knowledge, meaning that we consider the application first and foremost and will always try to understand the customer’s requirements. This results in a great match of product and application.”
AC Valve Alliance Group also offers engineering solutions so that it can modify valves in-house and provide specific configurations and construction materials to suit special applications and media. And, when it comes to new fuels, the company has recently developed valves for high pressure and/or low temperature hydrogen, helium and carbon dioxide, demonstrating that it can move with the times and embrace the move towards new fuels.
British valve manufacturer (and one of the brands stocked by AC Valve Alliance Group), Nacional Safety Valves UK is also looking ahead to the fuels of the future. Safety relief valve sales manager, Owen Stephens, comments: “With the use of hydrogen being part of the strategy of almost every major oil company, there’s a need to ensure safety relief valves are able of handling the potentially arduous operating and storage conditions; up to -253°c and 900 barg operating pressure.”
Continual innovation
As the fuel industry moves forward and depots develop, it’s reassuring to see how many manufacturers are rising to the challenge, responding to customer needs, and continuing to innovate.
We’d love to know how your depot has evolved and which products or services have made the biggest difference? Email liz@fueloilnews.co.uk
