Following the very mild winter of 2011/12, many pundits were predicting that 2013 would see a number of distributors exit the business. Largely due to a winter that extended up until May over which time sales of kerosene rose, this did not happen.
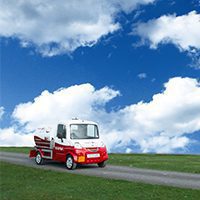
Ingoe’s brand new Tasca tanker
Although still a young company, Rochdale-based Ingoe Oils has big ambitions. Liz Boardman spoke to managing director and company owner, Jordan Ingoe about establishing the business and his plans for future expansion.A learning curve
Having bought the Fern Street Depot and existing fuel business in 2009, former industrial boiler engineer, Jordan, has taken time to immerse himself in the industry before really pushing the company forward over the last twelve months: “I am brand new to fuels,” he admits. “The last three years have been a massive learning curve for me. Although I already held Class 1 and 2 licences I’ve had to gain the necessary health and safety qualifications and ADR training and take on more staff.”
In addition to long-standing yard manager, Chris Quint and sales manager, Stephen Gomersall, Jordan has recently taken on sales advisor, Janet Thornton and a full time tanker driver, Brian Leach, who is bringing many years of experience with him, freeing up his time and allowing him to concentrate on developing the business further along with his partner, Rebecca who is also director and company secretary. “Over the last few months we’ve had some stumbling blocks to overcome and I’ve been doing all of the deliveries, but now I have a full-time driver, I can really focus on moving the business forward and increasing deliveries over the winter.”
With 70,000 litres of storage in brand new tanks from UK Bunded Fuel Tanks, fuel is currently bunkered in by BWOC and Tate Fuels. However the company has now started pulling out of Manchester Fuel Terminal.
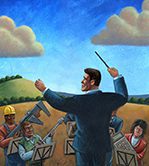
“Cultivating and nurturing a positive safety culture takes time and effort” says Jamie Elliott, human factors specialist, HFL Risk Services
Safety culture is essentially an organisation’s collective attitudes, values and behaviours towards safety. Put simply it is “how we do things around here” and in particular “how we do things around here when nobody’s looking.”
As companies working within the high hazard industries, oil and fuel operators’ safety policies are governed primarily by the COMAH (control of major accident hazards) regulations. Under these, operators are required to ensure that major accident risk potential remains as low as reasonably practicable. However, just because a company complies with industry safety regulations, it does not necessarily follow that it has a positive safety culture.
A staged progression – individuals, frontline workers, managers, directors and the board
Safety culture is often described as progressing through a series of stages. Early stages of safety culture maturity involve a focus on technical and procedural solutions to safety problems. When an incident occurs, the aim is often to find out who was involved.
As the organisation matures, managers increasingly realise that a wide range of factors cause accidents and that the root causes often originate from management decisions. This is where knowledge of human factors plays a key role. By understanding the individual, job and organisational factors that influence frontline workers’ performance, we can analyse individual human failures and determine what can be done to prevent them recurring. This moves the focus away from the individual who was in the wrong place at the wrong time, to look at what managers can do.
At higher levels of safety culture maturity, both frontline workers and managers co-operate proactively to prevent accidents and their root causes. So managers and frontline staff can drive safety culture from the bottom up by improving understanding of human and organisational factors throughout the organisation.
However, there is growing recognition that safety culture needs to be driven from the boardroom. Moreover employers in high hazard industries are increasingly being called upon to demonstrate organisational competence in process safety management. The UK Health & Safety Executive states that ‘Directors and boards need to examine their own behaviours, both individually and collectively’. Business leaders need to get out and talk to staff at all levels about process safety.
Setting Process Safety Performance Indicators (PSPIs) can be a structured way to do this. To be able to have these conversations, leaders need to have sufficient understanding of process safety including the root causes of accidents. If this is lacking then a first step is often to improve process safety competence at senior levels, not just in operations but also business support functions such as maintenance, HR, finance and quality at site and group level, as well as amongst non-executive directors.
Taking the time and effort to cultivate and nurture a positive safety culture will pay dividends not only in terms of overall site safety, but also in profitability since the two are very closely linked.
HFL Risk Services, which took part in last month’s Tank Storage Association exhibition and conference, offers nationally recognised qualifications for continuous improvement in process safety for senior managers and senior executives. www.hflrisk.com
European diesel and heating oil prices will be supported by a heavy autumn refinery maintenance schedule that is already prompting some interest to store product. But storage economics are looking uneconomic going forward, threatening thin cover for the winter, writes Chris Judge, senior products editor at Argus Media.
Whilst faltering economic growth in Europe in general, and in the UK in particular may improve diesel demand, the picture across Europe is still not encouraging for sellers.
The first half of 2013
Over the first half of the year diesel demand limped along, rarely achieving the margins sellers had hoped for at the start of the year, despite short episodes of market tightness. The weak demand in Europe is underlined by car sales that have been falling almost continuously for nearly two years, with supply boosted by refinery upgrades. More spot diesel volumes were expected from Spain and Greece, while Israel’s ORL started up a new 25,000 b/d hydrocracker at its Haifa refinery, Portugal’s Galp launched its own 43,000 b/d hydrocracker, and a slew of Russian refineries worked on expanded diesel production.
Nagging concerns over margins meant that European refineries – particularly those in the Mediterranean – continually trimmed output, keeping buyers on their toes, especially through the summer months.
Heavily reliant on imports
Refinery maintenance dominates on the supply side with weak motor fuel demand dominating on the demand side. A key source of winter diesel, Swedish refiner Preem’s 220,000 b/d refinery in Lysekil, Sweden, closed last month for six weeks of scheduled maintenance. Also on the docket for autumn works are Exxon’s 246,000 b/d refinery in Antwerp and unspecified units at BP’s 400,000 b/d Rotterdam refinery, and a variety of key Russian plants.
The UK is heavily reliant on imports from Europe following the closure of Russian product exports are expected to fall sharply from September to November as a result. The total capacity loss is forecast at 5.4mn t, with most of the cut coming in September-October, compared with 3.75mn t off line during the 2012 turnarounds.
Demand concerns persist. The seasonal downturn in driving and agricultural consumption is compounded by weak economic growth in Europe and forecasts that western Europe’s automotive market will not begin to grow again until at least 2019. That said, demand figures for the first half of 2013 were mixed. In much of northern Europe demand continues to grow, albeit at unspectacular rates – up 3% year on year in the first half in Germany and up by 2% in the first five months in Sweden. Troubled Mediterranean Europe saw drops of 6% in the first five months in Spain and 3.3% in Italy.
While traders and refiners expect the maintenance programme to provide support, it does not match the abrupt loss of 600,000 b/d of refining capacity with the insolvency of European refiner Petroplus early in 2012, when autumn premiums to the benchmark Ice gasoil surged to nearly $60/t and diesel’s crack spread against Brent surpassed $25/bl.
With the sale of all but one of the Petroplus refineries – the 146,000 b/d Petit Couronne in France seems doomed to permanent closure – most of the company’s former capacity is now back on stream. And, despite the general agreement that there is refining overcapacity in Europe, optimism over longer run prospects for diesel is driving plans for capacity additions; Italy’s ENI has already restarted its idled 105,000 b/d Gela refinery in Sicily. The company has also announced a €700mn investment plan, including diesel maximisation, in a bid to return the loss-making plant to profit.
More
Pete George, managing director, UK and Ireland marketing with Lindsay Grant, former manager, national sales, who will shortly be talking up a new role at Phillips 66’s Houston headquarters
Pete George, Phillips 66
“Phillips 66 plays a key role in providing a secure supply of petroleum products to the UK markets via its Humber Refinery. We are very pleased that the recent Energy and Climate Change Committee Inquiry: UK Oil Refining recognised the importance of oil products and UK refining to the UK’s economy. The report supported many of the recommendations that Phillips 66 made to ensure that UK oil refineries have a level playing field versus their international competition. In particular, the report recommended that:
Indigenous refinery production v inland market demand
Since 2000, diesel imports have risen from 16% of inland consumption to 44% and kerosene from 33% to 54%. By contrast, the share of motor spirit production exported has risen from 20% to 49% and that for fuel oil (including international marine bunkers) has increased from 55% to 95%. Exacerbating the motor spirit imbalance has been an increased import share, from 11% to 32%, which reflects the much expanded presence of the importing/wholesaling companies in the transport fuel sector (also a contributory factor in the rise of diesel imports).
Looking at the wider issue of import dependency, it is noteworthy that expert witness testimony to the recent Commons Energy & Climate Change Committee report was in broad agreement that a mix of domestically refined and imported products was essential for security of supply, the respective proportions being best determined by the market. So, the Committee advised DECC that, in its review, it should take an approach that reflects the integrated nature of indigenous refiners and importers as well as associated ancillary industries.
Is there substantive cause for concern?
Detailed below, the extensive physical infrastructure has been in place for many years, during which time it has been subject to much rationalisation. While enabling comprehensive market reach, it also has a commendable record of providing both security and continuity of supply, as well as helping the country to meet its compulsory stocking obligations.
The consequences, in terms of product supply dislocation, arising from disablement of the key Buncefield terminal in December 2005, bore testimony to the system’s resilience. That is not to say that there are not points of potential vulnerability; should there be loss of supply out of the Fawley refinery, the consequences for the South, the UK’s largest inland market region, are by far the most significant. The DECC review, to be completed by year end, is awaited with interest!
Most Read