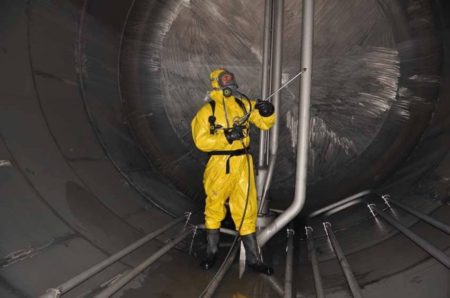
Emma Tilley, service and logistics manager for the group, explains their ‘people first’ approach and the role it plays in keeping operation disruption to a minimum.
“We recognise that we are in a people business,” Emma shares. “When something goes wrong, it causes problems for the people involved, which is why we focus on building strong relationships with our clients’ on-site teams.
“By prioritising these relationships, we can better serve our clients and help them avoid the significant losses associated with refuelling problems.”
A comfort blanket
“We get the job done, but it’s about more than that. We’re really proud of the relationships that we have with our service clients, and that’s testament to our team of service engineers.
“Our clients trust us to be there for them whenever they need us, like a comfort blanket that always delivers quality service.”
OTS has evolved a number of approaches that ensure any disruption created by equipment or system downtime is minimised to reduce business impacts as Emma elaborates.
“Our People-First objective ensures that our clients receive the best service possible while also minimising disruptions to their operations.
“We keep fuel storage and distribution systems running smoothly to support our clients’ success!”
Achieving first-time fixes
“We also focus on minimising downtime with our First-Time Fix objective that requires us to get our clients’ fuel storage and distribution systems back up and running as quickly as possible.
“In cases of reactive call outs, our service and logistics manager takes detailed information about the fault over the phone before the service engineers head out to the site equipped with the parts that we think will be most helpful.
“While there are some faults that require us to order parts that we don’t have in stock, our motto is ‘whatever it takes’, and we will move heaven and earth to get everything we need ASAP, and get the job done on the first site visit avoiding diagnostic-only call outs where possible.”
“We believe that prevention is always better than cure.”
As Emma notes: “I’m really proud of our service engineers. They work really hard, not just in a reactive way to fix problems that have been reported, but they take the time to have a look at the entire set up and to talk with the transport and maintenance managers on site. We believe that prevention is always better than a cure.
“This proactive approach is about more than just fixing immediate problems. We take the time to assess the entire setup and identify potential issues before they become major problems. By doing so, we can help our clients avoid unexpected downtime and prevent potentially costly future reactive call outs.”
A holistic approach
“We want to ensure that our clients are well looked after from every angle to minimise call outs and downtime,” Emma continues. “Our holistic approach includes prevention and education to give our clients a comprehensive service.”
And Emma notes the importance of the engagement between the OTS and client teams in meeting these expectations: “An important part of avoiding future faults is educating and empowering on-site staff. We take this approach seriously, and our service engineers are always available to provide advice and support to clients.
“We believe that a proactive approach to tank care can help our clients to avoid unexpected downtime and prevent costly call outs, so we also offer a Planned Preventative Maintenance Service (PPM). This helps clients identify and address potential issues before they become major problems.
“By combining education, prevention, and a responsive service to keep our clients’ fuel storage and distribution systems running smoothly we support our clients in delivering success.”
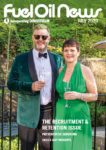