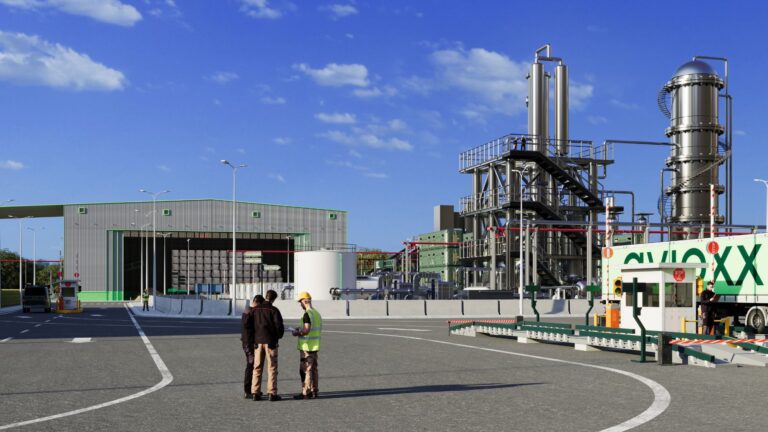
Emily Fung, Operations Manager, explained: “Avioxx has successfully completed a detailed design study of the novel Avioxx process for manufacturing sustainable aviation fuel from household waste. This in-depth analysis not only confirms the technical feasibility of the process but also provides an initial indication of the economic viability of commercial production.”
An essential step towards full-scale commercial production
“As part of the study, equipment sizing and capital cost estimates were also delivered for our 5,000 tonne-per-annum (TPA) large demonstration plant currently under development. The detailed design is an essential step towards realising a full-scale commercial production facility that will supply the aviation industry with sustainable fuel,” Emily continued.
“Process simulation tools enable engineers to digitally simulate real-world chemical processes under various conditions, which in turn helps to optimise production systems, assess economic viability, and reduce risk before committing to full-scale manufacturing. This initial study forms the basis for our engineers to further optimise their process for technical feasibility and economic viability at commercial scale.
“The process modelling also provides an important template for the analysis of the impact of market pricing and evolving regulatory measures around SAF. This helps ensure that Avioxx’s future production facility remains competitive and resilient in an evolving market for waste feedstock and sustainable jet fuel.”
An important breakthrough
Chris Hancock, CEO of Avioxx, highlighted the significance of the engineering milestone, stating, “This represents an important breakthrough and will give our investors added confidence that we will be amongst the first
globally to supply SAF at scale. We will be using wastes which are currently incinerated or sent to landfill, releasing vast amounts of damaging carbon into the atmosphere.
“The Avioxx process converts household waste into clean, sustainable fuels including SAF and renewable diesel. This is done via gasification and Fischer-Tropsch with a unique integration of solid oxide fuel cells (SOFCs) and electrolysers to increase efficiency and cost-effectiveness. The process design study is being conducted by our in-house team of
experienced process engineers and is currently being re-configured for different production capacities.”
A commitment to the transition toward green travel
Emily continued: “Our plans begin with the construction of a 5,000 TPA SAF manufacturing plant near Cheshire, UK, followed soon after by the first commercial unit, designed to supply 40 million litres of SAF per year to the aviation sector. We are targeting a sector that is under increasing pressure to decarbonise, and the ability to turn waste into a high-value product such as Jet A1 fuel could be a gamechanger for aviation. The company is currently backed by Trailfinders, the UK’s largest independent travel company, which sees the green transformation of air travel as an urgent mission.”
Image provided by Avioxx
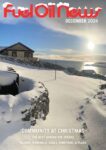