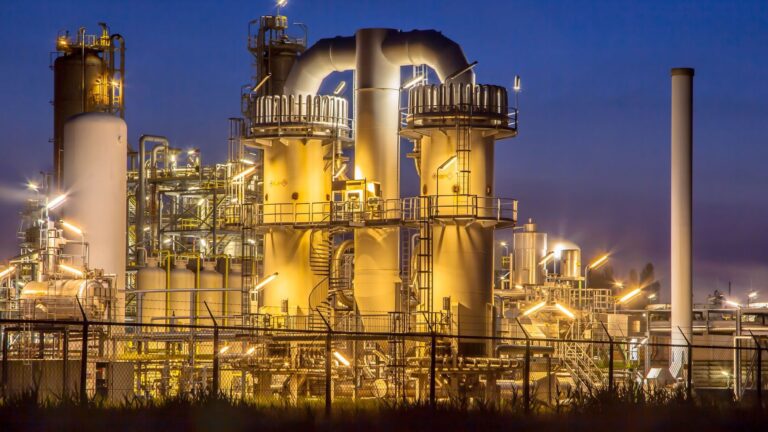
Whilst this, and reports from the ONS that indicate the UK economy is out of recession, are encouraging in the current economic climate, the industry still needs to overcome a variety of challenges if it is to put the future on a firmer footing.
Tim Doggett, CEO of the CBA, examines the current state of the chemical supply chain and discusses the industry-wide initiatives that are being implemented to reinforce it.
A critical industry
It is no overstatement to say that the chemical supply chain is one of the most critically important global industries. Not only does it play a role in the manufacture of over 97% of the world’s products; but innovation within the industry has led to the development of new materials, medicines, products and processes that continue to deliver enormous benefits across almost every other sector. Indeed, without the ongoing efforts of the chemical supply chain, modern life would come to a standstill.
As a result, when the supply chain faces disruption, the impact is widespread, preventing the production and supply of the goods that everyone depends upon. Fuel oil supply disruption, for example, would cause significant issues for the logistics and transport sector, and this, in turn, would have major repercussions for all the industries. This makes it vital that associations and stakeholders within the sector work tirelessly to address the issues that can lead to disruption.
Lasting effects of ‘Brexit’
The UK’s exit from the EU has resulted in a raft of challenges for chemical businesses on both sides of the border. Whether importing or exporting, adopting the formalities and administrational requirements that this created compelled companies to introduce new systems, processes and approaches
to business and trade with the EU. These changes have involved considerable time and resources, incurred additional costs and led to unavoidable delays. In some instances, companies set up entities in the EU while, in extreme cases, others simply discontinued certain trade lanes or moved their entire operations to the continent.
These changes are ongoing, with the second phase of the UK’s new Border Target Operating Model (BTOM) only coming into effect as recently as 30 April 2024. Aimed at protecting the UK’s biodiversity and predominantly affecting the food industry, it will also impact chemical companies that import plants and plant products as part of their production processes.
While it is designed to streamline customs processing, some smaller companies have said these new checks alone could cost them over £200,000 a year.
Besides adapting to new regulations, a further issue was the lack of infrastructure to support them. The lack of border patrol staff and checkpoint facilities, for instance, caused long delays at ports and roads being gridlocked. The checks that are now necessary have negatively affected ‘just in time’ supply chain models and any resulting delays impact production lines for businesses and potentially put perishable produce at risk.
Moreover, where infrastructure improvements have been made, the government is levying charges to pay for them. For example, April 30 saw the introduction of the Common User Charge for importers of animal products, plants and plant products to cover the cost of updated controls and systems.
Another ongoing challenge is the widening gap between UK and EU laws and regulations. With there now being both a UK and an EU REACH, multiple regulations can cause significant problems, complication and confusion, with companies potentially unable to source materials, export, import or manufacture them, or simply making them commercially unviable.
Brexit has also impacted the labour market, with fewer EU nationals now working in the UK. According to the University of Oxford’s Migration Observatory, the number of EU nationals working in the UK peaked at 2.66 million in 2019 and had fallen by 7% by 2022. At the same time, the new immigration system restricts the employment options of EU workers. This has led to a labour shortage in the chemical supply chain, with the lack of HGV drivers proving a specific problem, albeit a chronic and global phenomenon.
The effects of conflict
As a global industry, events in one country can have a direct and far-reaching impact on the chemical supply chains of others. The Russia-Ukraine war has been hugely disruptive, with both countries being major suppliers to the sector.
Sanctions on Russian suppliers, the closing of the Nord Stream 1 gas pipeline, the disruption to both land and Black Sea supply routes, army recruitment and the conflict itself have resulted in energy price rises, goods shortages, transport delays and labour shortages, especially with east European HGV drivers, many of whom are Ukrainian and who joined their military at the start of the war.
More recently, the conflict in the Middle East, particularly the attacks on shipping in the Red Sea has led to further problems. As a result, shipping lines are understandably reluctant to see their crews and vessels risk passing through the Suez Canal and have rerouted them around Africa, a move that makes transportation more costly, extends delivery times and impacts the productivity of vessels.
Additionally, any conflict in the Middle East also has the potential to affect global oil prices.
With so many challenges facing the chemical supply chain, industry stakeholders and the associations that represent them are developing partnerships and working with other organisations to implement a range of industry-wide initiatives to reinforce the sector. At the same time, they are embracing their responsibility as a voice for change, lobbying for practical solutions to today’s challenges.
Tackling UK REACH
One area of common concern is UK REACH. Here associations have played a leading role in assisting their members and the wider industry through lobbying and support. This has included lobbying the UK Government about the practicality and operability of UK REACH, as well as voicing concerns over the need to duplicate testing and costs to comply with UK REACH regulations.
After much perseverance, these efforts led to the Department for Environment, Food and Rural Affairs (DEFRA) agreeing to consult on extending deadlines and to consider a more workable and affordable model. This Government advocacy continues, with associations and other key organisations providing expert advice to the committees investigating a solution. In the meantime, associations are also providing their members with training, one-to-one advice services, and other resources.
Building a stable, skilled workforce Skills shortages are a potential issue for the chemical industry. There are several factors to consider on this, including the demographics and future retirement of skilled industry professionals, the lack of awareness of the careers and opportunities that are available, and a poor perception of the industry in general, in particular for younger generations.
Considering the spectrum of skills the chemical supply chain needs, addressing these factors now is vital for the industry’s long-term stability.
To attract new talent, associations, industry stakeholders and other organisations are working hard to change the way it is perceived. This includes countering the stereotypical views people have of it and promoting the valuable contributions it makes in virtually every aspect of our daily lives.
At the same time, there are efforts to establish the industry as an employer of choice, making young people more aware of the variety of careers the sector offers, the pathways to them, the long-term opportunities and the positive contributions they can make. Furthermore, work is taking place to improve retention by encouraging employers to offer vocational training, skills programmes and continuous learning options that lead to better career development opportunities for their staff.
With the younger generations increasingly seeking employment with businesses that are sustainable and which put equality, diversity and inclusion into practice, companies within the sector are updating their policies in line with these values, making them more attractive to future talent.
Initiatives for positive change
With regard to sustainability, for example, the Responsible Care (RC) programme is a long- established global initiative that provides an ethical framework for the safe and sustainable use and handling of chemical products.
Other initiatives are also bringing positive change. The CBA People & Skills Hub (P&SH), which unites stakeholders from across the sector with education partners, thought leaders and sector experts, has been successful in fostering knowledge sharing, skills development and career development opportunities.
Participants, also have access to outreach programmes, resources and networking opportunities. The CBA Future Council, meanwhile, enables young industry professionals to share knowledge and experience of the wider supply chain. It also holds events to promote the sector and in 2023 alone, it engaged with over 17,500 young people at over 25 events.
Generation Logistics is an industry led initiative that seeks to improve recruitment by raising awareness of the career opportunities right across the logistics industry, including not just roles in HGV driving, but also warehousing, engineering, IT, sales, marketing, HR and much more. Supported by the Department for Transport and involving more than 40 prominent associations and organisations from across the sector, it aims to promote the various pathways into the industry, such as direct entry, apprenticeships and graduate programmes. Highly successful during its first year, the campaign reached 3.3 million engagements by September 2023.
Another similar initiative launched by the CBA, Generation STEAM, has a goal of inclusivity and to ensure young people are empowered to build bright futures in the chemical supply chain industry, regardless of their background and skills. Generation STEAM adds the letter A to the traditional STEM focus, with A standing for Arts, or indeed other words such as Ability, Attitude or Ambition.
This reflects the need for creativity and innovation within the chemical supply chain and aims to attract a broader spectrum of talent that the industry needs in today’s world – and in the future – especially as Artificial Intelligence only continues to rapidly evolve and expand.
The CBA 5050Vision
Organisations such as the CBA are not only focusing on future generations and recognise the merits in embracing seasoned professionals, over the age of 50 and that employers must create a workplace that values and utilises the talents of all employees, regardless of age.
The CBA 5050Vision highlights the value of this segment of the workforce and showcases the benefits of retaining and actively engaging with these experienced individuals, who can offer a wealth of knowledge, expertise, and institutional insight, whilst driving innovation, enhancing safety protocols, and mentoring the next generation of talent. At the same time, it is looking to attract those that may be returning to work after a career break or indeed looking for a career switch.
Throughout its long history, the chemical supply industry has always had to overcome challenges, not least, two world wars and the Great Depression. Most recently, however, major challenges like the pandemic, Brexit, skills shortages and the conflicts in Ukraine and the Middle East have come in rapid succession, each bringing their own issues.
As a proactive association, the CBA actively supports its members and the industry at large in addressing today’s challenges.
In doing so, it represents and lobbies for the industry at the highest levels, implements initiatives that provide tangible benefits and delivers vital training and advice.
Image credit: The Chemical Business Association
Image of Tim Doggett supplied by Shrewdd Marketing for the CBA
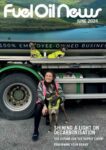