The company’s first major expansion occurred at the end of the Second World War with the easing of wartime restrictions on the sale of oil and petrol. On the 1st of January 1947 Robert Rix’s eldest son, John Robert Rix, the grandfather of the present chairman, formed J. R. Rix and Sons with a working capital of £7,000 and one motor ship. Supplying agricultural and commercial diesel customers throughout Yorkshire’s East Riding, ‘old man Robert’, as he was fondly called, also established petrol filling stations in the Hull area.
Fast forward to the present day and Rix Petroleum is one of the oldest remaining family- owned, independent fuel distributors in the UK. The company distributes and retails petroleum products to homes and businesses from local branches located throughout Yorkshire, Lincolnshire, Mercia, Midlands, North East, East Anglia and Essex. Rix also has three fuel depots throughout Scotland: in Grangemouth, Aberdeen and Montrose.
Enhancing the customer experience
The fuel distribution system at Rix Petroleum is fundamental in maintaining its high levels of customer service. The previous IT system had served the company well for a number of years but did not provide the flexibility to support future company growth. As a result, Rix was looking to source a new system to optimise the entire fuel delivery process.
The solution
Designed specifically for the petroleum sector, Rix selected a new system from TouchStar Technologies. The core of TouchStar’s ‘FuelStar’ system is P.O.D. software that is designed to digitise the entire process from loading to delivering and electronic confirmation. The system utilises ATEX-certified in-cab computers which fulfilled Rix’s requirement for a device with a large, driver-friendly touchscreen. The in-cab computers were ideal for the RIX operation as they provided a robust, real-time link between the vehicle and the CODAS back-office system.
Duncan Lambert, managing director for Rix Petroleum, reflects on that period of the company’s development: “The benefit of the new system was that it allowed us to provide a single and enhanced means of communication between ourselves and the driver. Our investment meant we had an efficient way of communicating to the driver and the ability to receive communication back, in real time, which was not possible with a manual paper-based system”.
The development of the solution
Rix Petroleum worked in partnership with TouchStar and CODAS to ensure that the original system delivery dates were achieved. Sam Stanley, IT project leader for the new system implementation explains: “Considering this was a brand-new system for us, we were very impressed with how smoothly it went when the system went live. This was helped significantly by the comprehensive induction that took place, enabling the drivers to fully buy into the new system”.
How the system works
Pre-shift
Sales orders are taken by phone and entered into the CODAS back office, which allows for the job to be allocated to a specified driver. Building loads is simple. Orders can be rapidly entered then scheduled and sent directly to the driver on the TouchStar in-cab computers. RIX now has the ability to view the deliveries via the FuelStar mapping console which enables them to consolidate deliveries more effectively.
The driver of the vehicle is required to complete the start of shift procedure before commencing the deliveries for the day. Prior to gaining access to the trip details the driver is required to complete a vehicle safety check.
The safety checks are designed around DVSA standards and are configurable on a ‘per client’ basis.
Vehicle loading
As part of the log on procedure, a totaliser reading is taken from the meter providing automatic verification data of the truck and stock status. Upon completion, the driver is instructed by the on-board computer what grade and volume of fuel to load onto the vehicle and confirm loading into each compartment of the vehicle. The system also captures the BOL (Bill Of Laden) numbers supplied by the loading gantry system.
Fuel delivery
On arrival at the customer site, the driver then commences the unloading of the fuel. The flow meter connects with the TouchStar in-cab computer to record the volume of fuel that is being delivered. The connection with the meter provides a confirmation of exactly what has been delivered and the balance of fuel that remains on the vehicle, allowing for a real-time up-to-date stock manifest. At every stage the system guides the driver through a HSE questionnaire to ensure the driver performs the delivery safely.
Proof of delivery
Upon completion, the delivery information is updated on the TouchStar in-cab computer producing a delivery confirmation. The driver can hand the device to the customer to confirm the delivered quantities and sign on-screen.
Connectivity to the in-cab printer then produces a signed receipt for the customer. Using GPRS communication, the delivery data is transmitted to the back office providing real time proof of delivery.
Speaking about the benefit of the system, Duncan Lambert comments: “Confirming the customer name, capturing the signature and communicating it to the back office in real time significantly speeded up the invoicing procedure. The system enabled us to respond to customer invoicing queries quicker which ultimately benefited our business with improved cash flow.”
Real-time improvements
The system now delivers performance information relating to number of deliveries per day, distance travelled per vehicle and volume of fuel delivered. The real time information that the system provides has been invaluable in allowing Rix to study and compare vehicle performance and overall delivery efficiency.
Duncan continues: “We can physically see the improvements that the system has made to our operation, and this is a big step forward in the business. We have absolute confidence in the accuracy of the data we receive back from the system”.
What’s next?
RIX is continually examining ways in which its systems can provide even more benefits to the company and its customers. Having run the TouchStar system for a lengthy period of time, the company was diligent in re-examining the competitive marketplace. Duncan Lambert comments: “Although we were not dissatisfied with the performance of FuelStar in any way, we were obligated to ensure that our business is operating with the most effective systems that we can acquire. As such, we conducted a thorough re-evaluation exercise which included the trialling of alternative suppliers in certain depots. I’m happy to say that our original decision to adopt the TouchStar solution was fully vindicated, as it is clearly still the market leader.”
Bespoke industry systems
TouchStar hardware and software solutions are specifically designed for the fuel distribution industry. The company has invested heavily in the development of a new range of terminals based around the Android operating system. This platform offers multiple technical benefits over previous generation Windows CE devices and, as a progressive organisation, RIX readily accepted TouchStar’s suggestion to upgrade their fleet hardware.
The new devices will remain integral to the fuel delivery operation but also offer significant additional benefits. For example, the in-cab computers will now operate as phone devices which will preclude RIX having to invest in, and maintain, separate SIM cards. The company will also be able to run additional business applications directly on the in-cab device including HSE and training-related software.
After initial trials of the Android terminal at two depots, RIX now intends to roll them out to its entire fleet of one hundred vehicles. The implementation phase commenced in September 2022.
Duncan concludes: “We expect to avail ourselves of many additional benefits to the business based on the Android OS and the new FuelStar application. The system creates a great opportunity for RIX to expand the connectivity and visibility between the truck, product, driver and the planning office.”
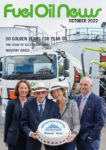