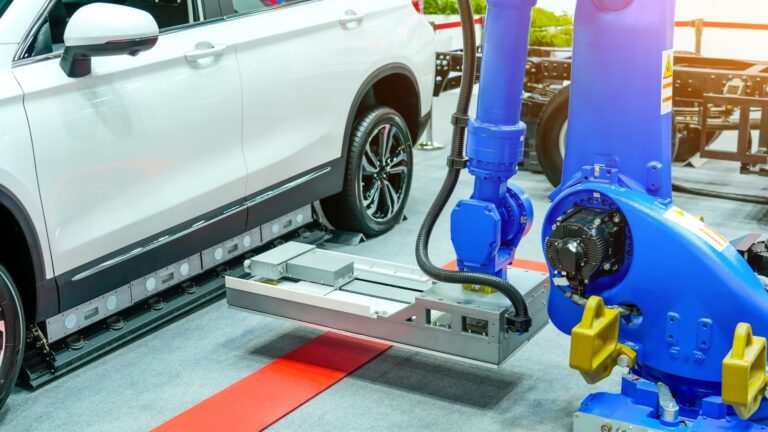
Amongst several fundamental problems, a lack of on-road charging infrastructure, coupled with the time taken to charge constantly operating vehicles were the main arguments against truck electrification.
But what if there was a way of bypassing charging infrastructure and at the same time, massively reducing the time taken to replenish batteries?
Whereas Europe’s chosen path (and to a lesser extent the USA) has been to follow the charging infrastructure model, China (the biggest HGV market in the world) is now full steam ahead towards a very different vision – battery swapping!
Gone are the requirements for a costly network of mega-chargers, making huge demands on the grid and rapidly degrading truck batteries because of the speed of charge required (for optimised operations).
Instead, an increasing number of Chinese trucks are simply swapping “flat” batteries for ready charged ones, all in the space of 5 minutes!
Clearly, there are significant advantages with this method. Firstly, the batteries do not require charging then and there, so can be charged “at leisure”. This not only costs less but significantly extends the battery’s life.
Furthermore, because the batteries are not integrated into the truck itself, they are owned by the charging station and effectively leased to the truck operator. This reduces the initial cost of the truck and means that the life of the battery is disconnected from the service level of the truck, which hugely improves the residual value of the vehicle (see last month’s report on funding of trucks and residual values).
It also highlights a significant divergence in the type of trucks being manufactured in China versus the West. EU and US truck makers have continued to integrate batteries into the chassis of their vehicles (which makes battery swapping nigh-on impossible), compared to the separated battery location increasingly being adopted by Chinese e-truck makers.
None of this is to say that interchanging a 7.5 tonne battery is a straight-forward and simple process. The battery-swapping centres must also act as a charging hub, which necessitates industrial level connections to the grid.
Furthermore, the weight and risk (pierced batteries) involved in the process requires total robotised automation which, when added to heavy duty cooling requirements (to stop over-heating) and fire safety obligations, means both the initial capital investment and ongoing operating costs are substantial.
It is however, still considerably cheaper and quicker than installing hundreds of thousands of individual chargers up and down the road network. In this light, mega-charging sites, set-up at already established logistics / warehouse hubs would seem a practical and cost-effective solution.
Once again, the proof is in the pudding and there seems to be ample evidence that this method of HGV electrification is beginning to get traction. In 2020, there were 500 battery swap stations in China. By 2023, that number had increased to 3,500 and this year, it is estimated that the number will be in excess of 35,000.
Of course, these sites still serve a small proportion of the 2.4m heavy trucks in China (over 90% of which are still diesel powered), but a 900% increase in swapping centres over a 2 year period is probably a trend that shouldn’t be overlooked!
Of course, there is a total logic in China adopting battery swapping technology. Anyone who has followed the journey of automotive electrification will know that China dominates the sector and (to be frank) has set out to dominate from the start.
Initially they hoovered up the mineral extraction rights for precious metals such as lithium and cobalt. Then they cornered the refining and processing industries to convert those metals into batteries (90% of lithium-ion refining takes place in China), before going on to perfect the battery technology.
Finally, they transferred that technology into electric vehicles and predictably, ascendancy in the electric automotive sector has followed; 65% of the global e-car pool, 90% of e-buses and now 80% of e-trucks all come from China…
For many, these figures are worrisome in the extreme, as they point to complete reliance on China for electric vehicles. It is ultimately this fear and the long-term consequences for western automotive manufacturers, that might ensure HGV battery swapping never takes off in Europe or the USA.
If that was the case and EU / US manufacturers doggedly stick with the charging infrastructure model, then e-trucks seem an unlikely pipedream, with all the issues we raised last month presenting continual obstacles.
European governments are already behind their targets for full car electrification (the UK requires the installation of 100 new public chargers every day for the next 10 years to meet its 2035 target) and so, turning attentions to the more complex job of truck electrification (frankly) feels unlikely.
Either trucks will stay with internal combustion engines, or the West will have to accept battery swapping and the inevitable domination of Chinese trucks and technology.
Image credit: Dreamstime
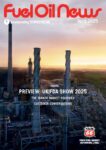