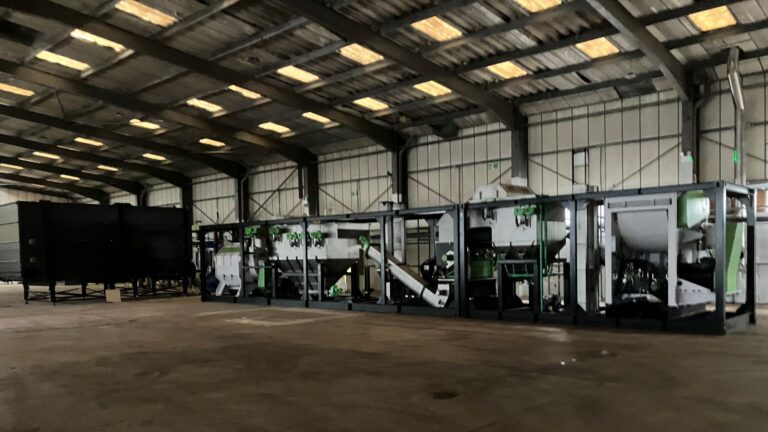
Tim StClair-Pearce is the Co-Founder of QM Recycled Energy (QMRE), a company whose sole focus is to find an environmental solution to end-of-life plastics to reduce plastic pollution.
Channelling almost four decades of experience in the plastics, paper and packaging industries Tim is helping to provide a solution for one of the most pressing environmental problems facing society today – how to deal with the millions of tonnes of plastic waste created every year.
Margaret Major, Publishing Director for Fuel Oil News, met with Tim to find out more about this solution and why the fuel industry is becoming increasingly interested in its possibilities.
QMRE is currently undertaking a nationwide roll-out of dedicated plastic to energy recycling centres which will use proven technology to turn plastic waste into valuable hydrocarbons.
QMRE’s story begins with a challenge – tackling the inefficiencies in plastic waste recycling. Tim StClair-Pearce recalls an initial meeting with Kent County Council, where he questioned their claim of 95% efficiency in waste management. Further investigation, revealed that only 9% of plastic waste was actually being recycled, with the majority going to landfill, incineration, or export. This revelation set him on a journey to find a viable solution to the growing plastic waste crisis.
Travelling across the globe, the QMRE team examined existing recycling methods. In China, they encountered an industry struggling with inefficiencies, where converting plastic to oil required more energy than it produced. Pyrolysis was showing promise but lacked the efficiency to be viable. The key takeaway from this phase of research was the need for a continuous process – one that could operate efficiently without excessive energy consumption or emissions.
Developing the QMRE technology
After extensive research, QMRE found an experimental model at Dresden University that aligned with their vision. They commissioned a pilot machine for around €200,000 and tested it in the UK. Despite initial scepticism from industry giants like BP, QMRE successfully proved the technology’s potential, even receiving an apology from a BP representative after the results were showcased on the BBC News at Ten.
A key refinement of the process was to move from traditional pyrolysis to what they refer to as thermolysis – a cleaner, more efficient method that avoids direct combustion. Instead, the system captures and reuses the non-condensable gases to power itself, reducing emissions and increasing efficiency.
The feedstock is plastic waste – particularly soft plastics – for which the waste industry has no answers. No two plastics are identical and can’t be mixed up, so they don’t know what to do with it and it ends up in what is called belt stock.
Belt stock is piled high in many, many counties because if it is incinerated, the resultant high levels of emissions will shut down the generator. Needing something like 30 tonnes of fuel oil to get the generator going again, waste licenses are jeopardised.
As Tim StClair-Pearce explains: “A solution was needed that didn’t involve burning the product, so we derived a solution based on pyrolysis that we call thermolysis because pyro means fire, and we don’t use fire. Lysis is separation.”
“We trap the light gases that are non-condensable and feed them into a genset generator and it provides 70% of our power. So, we have very little waste, and we have very little coming into the site.”
How it works
QMRE’s process takes one kilogram of plastic waste and converts it into one litre of usable oil. About 12% of the original material is converted to gas, which is then used to generate 70% of the energy needed to power the system. The remaining 3% becomes carbon ash, which is repurposed into road-building materials through a partnership with Associated Asphalt.
Unlike conventional waste processing, QMRE’s system does not rely on large, centralised plants. Instead, their modular model allows smaller facilities to be set up closer to waste sources, reducing transportation emissions and costs. This approach aligns with their goal of building 100 sites across the UK, each capable of processing 10-20 tonnes of plastic waste per day, collectively addressing 10-20% of the country’s packaging waste.
Turnkey solution
QMRE provides a comprehensive turnkey solution for businesses and organisations looking to process plastic waste efficiently. The company offers a ready-to-operate processing unit, handling everything from site setup to staff training and ongoing technical support. This makes it an attractive proposition for waste management companies, industrial sites, and organisations seeking to reduce their environmental impact while benefiting from the financial incentives of converting plastic waste into valuable fuel.
To set up a QMRE processing unit, customers need approximately one acre of land and an investment of around £7.5 million for a fully operational facility with four VIXLA systems. Each unit is designed to handle 5 tonnes of plastic waste per day (a total of 20 tonnes), providing a scalable and profitable solution for waste processing and fuel production. Within three years, customers can recoup their investment through oil sales, RTFO credit earnings, and operational efficiencies.
QMRE also assists clients in securing long-term contracts for their output, whether in the plastics or fuels market. Customers can choose to sell their recycled oil to a major petchem, or plastic manufacturing or supply it to fuel blenders and refiners looking to integrate sustainable alternatives into their fuel mix. QMRE’s expertise ensures that every client has access to the most profitable and sustainable pathways for their end product.
Commercial applications and partnerships
QMRE has secured an offtake agreement with a major petchem for the recycled oil which will be used in the production of renewable plastic.
While QMRE’s ambition is the creation of a fully circular plastics economy with net zero emissions, the process is also proving attractive to the fuel sector, where it can contribute to the production of both sustainable aviation fuel (SAF) and low-emission diesel. With regulatory approvals progressing, the company is working to integrate their recycled oil into the DfT Renewable Transport Fuel Obligation (RTFO) scheme, making it an attractive alternative for fuel suppliers.
The RTFO presents a highly lucrative opportunity for QMRE, as the oil produced from plastic waste qualifies for credits under the scheme. These credits act as incentives for fuel producers to incorporate renewable and sustainable fuels into their supply chain, with significant financial value attached to them. Currently, each RTFO credit can be worth substantial amounts, and with the inclusion of refuse-derived fuels now formally recognised, QMRE stands to benefit from this growing market.
By producing oil that can be blended into diesel and other fuel types, QMRE’s process can provide a sustainable alternative to fossil-based fuels while also ensuring that waste plastics are removed from the environment. With an estimated 83 billion litres of diesel used annually in road transport alone, even a small portion of QMRE’s recycled oil entering the market could have a meaningful impact on reducing emissions and reliance on crude oil.
Partnerships with fuel blenders and distributors
Additionally, companies looking to meet their net-zero targets are actively seeking alternative fuel sources that align with government incentives. QMRE’s ability to generate RTFO-eligible oil positions them as a key supplier in the evolving fuel market. As the demand for lower-carbon fuels grows, the value of these credits is expected to increase, making it even more profitable for companies to integrate QMRE’s oil into their supply chains.
There will also be an opportunity for partnerships with fuel blenders and distributors who can take their product and incorporate it into commercially available fuel blends. With the right certifications and further advancements in refining technology, this oil could soon become a mainstream component of transport fuels, aviation fuels, and even marine fuels.
Additionally, QMRE is exploring solutions for specific plastic waste streams such as carpets and astroturf, products which are challenging to recycle conventionally. Their trials with carpet manufacturers demonstrated a 60% oil yield, with the potential to create a circular economy where old carpets are turned back into new materials. Other potential areas of interest would be NHS and farmers’ plastic waste.
Challenges and the road ahead
Despite rapid progress and excellent results, QMRE faces significant barriers to scaling up. Government support remains minimal, with no public funding received to date. Regulatory hurdles also slow down the adoption of innovative recycling technologies. The team continues to engage with policymakers, pushing for recognition of their process within existing waste management and renewable energy frameworks.
As demand for sustainable waste solutions grows, QMRE’s approach offers a scalable and profitable model that can be replicated globally and the company’s vision extends beyond the UK, with partnerships forming in Spain and Portugal, Belgium, Luxembourg, Holland and France, Nigeria and South Africa.
A circular economy for plastics
Ultimately, QMRE aims to create a fully circular plastic economy—taking waste plastics, repurposing them into new materials, and reducing reliance on virgin fossil-based plastics. While some of their product may enter the fuel market, their primary mission remains clear: to eliminate plastic waste and transform it into valuable, sustainable resources.
With private investment driving their expansion and increasing industry interest, QMRE is well-positioned to disrupt the plastic recycling landscape, proving that waste can be transformed from a problem to a solution.
Image supplied by QMRE
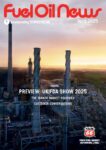