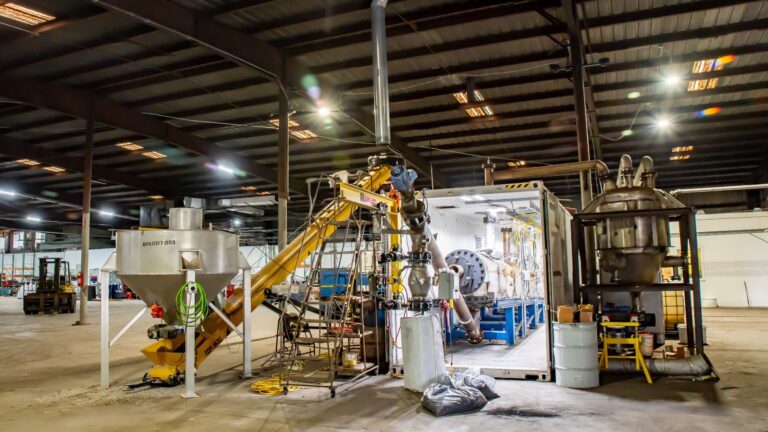
The company was founded by Canadian actor turned inventor Brian Ablett, who has worked with a group of engineers in rural Southern Alabama to solve the environmental, practical and commercial challenges of pyrolysis (the process by which waste plastic is converted to fuel). The resultant fuel has the potential to transform sustainability in transport by delivering an alternative fuel that is less environmentally polluting, more cost-effective, and solves the UK’s massive waste problem.
Brian is incredibly passionate about the potential of his technology to help to reduce the UK’s reliance on fossil fuels and spoke with Fuel Oil News to explain how the AHFL approach was developed and what it offers, as well as addressing the barriers to adoption and the plans for the UK facility.
In 1874, British engineering firm Manlove, Alliott & Co. created the first “destructor”. This new device, designed and patented by Alfred Fryer, was created to dispose of waste piling up across the UK’s major cities in an easy manner: by burning it. Ever since, incineration – as the technology is now called – has remained a staple of any municipal waste management strategy across the world. As our cities get larger, and rubbish keeps piling up on the sides of streets, pyrolysis has emerged as a quicker and cheaper alternative to packing waste into ever-expanding landfills. More importantly, it’s been seen as a more ethical and environmentally friendly alternative to exporting it to be dumped in another country – or into our nearest water bodies.
The invention of plastic in the last century, and its spectacular rise as the most omnipresent material in modern society, has raised serious questions about our continued ability to turn to incineration as a way to manage waste disposal. Unlike organic waste, plastic releases hundreds of noxious chemicals into the air when burnt and leaves a residue that is equally toxic and difficult to get rid of. Given the staggering amounts of plastic we consume – almost 400 million metric tons of plastic were produced globally in 2022 alone – alternate methods of plastic waste disposal have also come up short in our search for a truly sustainable solution.
From the Arctic to the Antarctic, microplastics have now been found in the remotest corners of the Earth. We are confronting what can only be described as a global plastic crisis. How do we get ourselves out of the mess we’ve created?
From recycling and reuse to regeneration
Incineration has been the only scalable alternative to landfills so far but has come under fire (pun intended) for swapping one form of pollution for another.
Environmental activists have pushed for recycling as a better alternative, arguing for a “waste hierarchy” that prioritises creating a circular economy for plastic waste where older plastic is recycled to serve our demand for new. They have also pushed to reuse plastic wherever possible, emphasising finding innovative uses for plastic waste that do not require further processing or chemical alteration.
While these solutions may be appealing on an individual level, they are a drop in the ocean if we are to seriously tackle the systemic problem of plastic pollution. Today, less than a fifth of plastic waste is recycled, and an even smaller percentage is reused. What’s worse: both recycling and reuse are exorbitantly expensive and labour intensive, making them unviable solutions in the present economic conditions. And they require extensive segregation of waste in the initial stages, making them unfit for tackling the mounds of plastic waste that currently surround us.
The last three decades have seen the emergence of chemical recycling technologies that aim to transform plastic from a waste into a resource. Initially accused of being a part of the plastic industry’s “greenwashing” tactics, these technologies have made significant progress to create a template – most crucially – for converting plastic into fuel while finding effective ways to contain or dispose the toxic by-products of the chemical transformation.
While earlier forms of chemical recycling technologies used more crude forms of incineration, which released toxic fumes into the working-class neighbourhoods where plants were located, newer technologies have offered a cleaner, greener way to dispose of plastic waste in light of more stringent regulations.
However, there remain certain challenges to this type of process that have yet to be overcome. These include the substantial energy demands inherent in the process, the necessity for chemical catalysts, and the emissions produced by the involved plants. Moreover, most systems grapple with the recurrent need for shutdowns to mitigate the accumulation of residue. The final output often manifests as a wax-like substance, necessitating further processing in a refinery to yield either plastic or fuel. Notably, a substantial proportion of these initiatives fail to achieve profitability, relying on recurrent injections of capital to sustain their operations. This raises pertinent questions about the long-term viability and economic feasibility of such endeavours.
Commercially viable solutions
In 2010, I saw an opportunity to tackle the plastic crisis in a commercially viable manner. I had just put together a consortium of manufacturing and engineering companies in response to the Deepwater Horizon accident in the Gulf of Mexico. Oil Containment Systems Inc further developed a high efficiency, low-cost plastic film – which I developed and patented with the original inventor, during efforts to contain the Exxon Valdez incident with the assistance of the Canadian Government – to put into action a rapid, efficient clean up and containment of oil spills.
While I was in the Gulf of Mexico in 2010, conversations with scientists, industry leaders, and environmentalists made me realise that not only was an alternative to older forms of chemical recycling possible – but it was also profitable. Four years of research and development later, Advanced Hydrocarbon Fuels Limited was born. With a business-first approach towards tackling plastic waste, AHFL has created the world’s first commercially-viable technology to make fuel from plastic.
Our exclusive time-temperature control system enables the utilisation of diverse, mixed plastic feedstocks, including post-consumer, post-commercial, and post-recycling plastic and extending to end-of-life waste plastic in oceans. This innovative approach holds the potential to effectively address plastic waste on a global scale. Validated by a proof-of-concept certification from renowned engineering firm Wood PLC, our modular processing lines boast 24/7 operability and can be installed cost-effectively to adapt to fluctuating plastic processing volumes. Crucially, our method achieves plastic breakdown through energy-efficient gasification at lower temperatures, avoiding harmful emissions associated with earlier technologies. Our system also operates without a catalyst, eliminating the risk of emitting hazardous chemicals linked to catalytic pyrolysis and other unsustainable techniques. The result is an environmentally friendly, scalable, efficient, and economically viable process capable of producing substantial quantities of low-carbon footprint fuel, even from the most challenging-to-recycle plastics.
The main alternatives to plastic feedstocks are biofuels, which offer a somewhat cleaner alternative to fossil-based fuels. However, the ever-growing biofuel feedstock requirements have led to widespread deforestation and impacted wildlife conservation and carbon absorption strategies. Use of feedstocks like corn has driven up the cost of food worldwide, harming availability in developing countries.
Keroclean®
Over the last few decades, attempts to transform plastic into energy – be it through pyrolysis or other methods – have proven to be a wild rollercoaster of inefficiency, sky-high costs, lacklustre productivity, and, in some cases, perilous adventures in sustainability.
AHFL is here to change that. More than 60% of the output of our lines is fuel, compared to typically less than 40% for other processes. Keroclean®, our trademark fuel, can be mixed with diesel to power everything from industrial power generators to heavy machinery at significantly reduced costs and emissions. A single AHFL line can produce up to 21 million litres of fuel per year, processing a minimum of 2 metric tonnes of waste plastic per hour.
35% of the gas produced through our lines is recycled to power the plant itself, making our technology practically self-sufficient and allowing it to function almost entirely off the grid. This means that modular AHFL lines can be installed anywhere – from airports to landfills. The final 5% of the AHFL process output is an ash that can be used in paving.
Keroclean® is a game-changer as it allows for a pragmatic, phased solution to the plastic crisis. We know that the long-term solution for plastic pollution is an end to plastic production and that the long-term solution to climate change is a complete turning away from traditional fuels. However, in the meanwhile, we cannot stop finding innovative ways to make existing processes more efficient and sustainable until a permanent solution is found.
By tackling plastic that already exists in the environment – in landfills, municipal waste units and oceans – AHFL aims to tackle the plastic crisis at scale. More importantly, given that equipment – from tractors to marine transport vehicles – isn’t likely to be replaced overnight with alternatives that use more sustainable fuel, our focus is on ensuring that Keroclean® can be mixed with diesel to power existing machinery without the need to replace their engines.
Looking to the future
According to a 2022 OECD report, plastic waste is projected to almost triple by 2060. Each day wasted in finding a perfect solution, then, results in unprecedented amounts of plastic piling up in landfills, entering our waterbodies, and seeping into our topsoil.
International efforts to tackle plastic pollution are progressing slowly, but surely, towards innovative problem solving. An Intergovernmental Negotiating Committee (INC) under the UN Environment Assembly has been set up to develop an international legally binding instrument on plastic pollution – including in the marine environment.
The UK is playing a decisive role in these negotiations, making alternative fuels a priority in discussions around national energy policy. In November 2023, a Virgin Atlantic flight made history by becoming the first transatlantic flight to operate entirely on Sustainable Aviation Fuel. This was made possible through support from the DfT(which has also set up an ambitious Advanced Fuels Fund) and partners within the corporate world and academia.
In the face of a favourable regulatory atmosphere and bolstered by a sense of greater global urgency around the plastic crisis, I am confident we will deliver upon our promise of creating a commercially viable way to transform plastic into fuel. Our demonstration line processes 1,000 pounds of mixed plastic waste per hour, producing 650 pounds of fuel. Our full production line will process at least 4,000 pounds per hour – possibly considerably more.
There are unarguable reasons why plastic waste needs to be removed from our ecosystems now rather than later, allowing us to reclaim our land and oceans and stop plastic further infiltrating our food chain. Our approach will be price competitive with fossil fuels in all applications and will not require subsidies or carbon offsets to achieve similar results.
At AHFL, we believe that addressing the world’s plastic waste problem needs to start now and work alongside the nation’s decarbonisation projects.
There is no alternative.
Brian Ablett is a UK-based inventor and entrepreneur who began by starting companies, as a teenager, in his native Canada. In addition to Advanced Hydrocarbon Fuel Ltd, Brian has founded Oil Containment Systems Inc, a high efficiency, low-cost plastic film for rapid response to contain and clean up oil spills, and Brian’s Glove Project Ltd, in partnership with a leading UK university, developing and marketing an original concept product to reduce the spread of MRSA in hospitals and lower the impact of SARS, and over 50 other companies, developing new products and technologies.
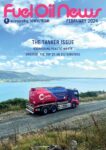