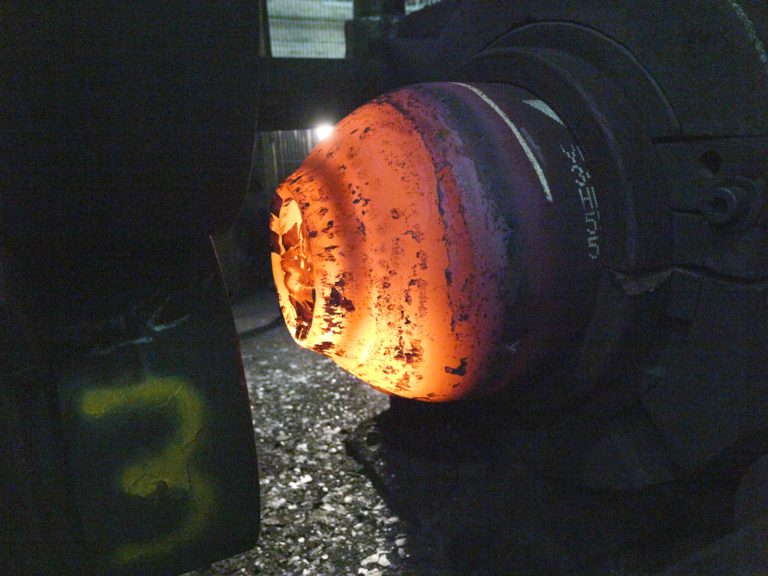
Engineers from the AMRC and the University of Sheffield’s Energy Institute are working with energy company E.ON, Chesterfield Special Cylinders, Glass Futures and Sheffield Forgemasters to explore ways to generate green hydrogen at the Blackburn Meadows renewable energy park, which could then be used as a cleaner fuel source for Sheffield’s steel industry, alongside other energy-intensive industries.
Government-funded
The pioneering project, funded by the Government Department of Energy Security and net zero and its Net Zero Innovation Portfolio (NZIP), could cut carbon emissions from Sheffield’s steel industry by 40%.
The initiative has been awarded an additional £1 million of government funding – one of only two to receive such funding – to continue to a second phase to explore the commercial and engineering needs of generating, transporting and using hydrogen – as well as developing the commercial offer to industrial customers. If successful, the next stage will see a technical pilot project begin at the Blackburn Meadows site – with the potential for future expansion if the project is taken forward to a fully commercial demonstration.
Industrial decarbonisation
Stuart Dawson, the AMRC’s chief engineer for hydrogen, who is part of the project’s technical steering committee, said that enabling fuel switching from natural gas to low carbon hydrogen is critical to decarbonising high temperature industrial processes that can’t be electrified.
He added: “Over the past 20 years, the AMRC has been the catalyst for the regeneration of manufacturing within the region. Now, we also need to be the catalyst for sustainable manufacturing and this industrial decarbonisation project exemplifies this.
“By working with local industry, the University’s Translational Energy Research Centre (TERC) and our Energy Institute, we are providing the combustion modelling expertise to accurately predict the thermal performance and emissions of Chesterfield Special Cylinders forging furnaces if they were to be switched from natural gas to hydrogen and also the comparative performance of three new hydrogen compatible burners designs.”
An earlier feasibility study, which concluded in February, found that fuel switching steel furnaces to green hydrogen could be commercially viable and sustainable over the longer term. It could maintain furnace performance and product quality for the steel manufacturers, but with carbon emissions estimated to be 41.8 % lower than if using natural gas. That means the three manufacturers taking part in the initial trials could save around 3,500 tonnes of CO2 each year.
Professor Mohamed Pourkashanian, OBE, head of the University of Sheffield Energy Institute, said: “We’re thrilled that this project has received funding from the UK Government to progress to a second stage. The work we’re doing for this project at the University of Sheffield Energy Institute, including computational Fluid Dynamic (CFD) modelling and in-depth hydrogen research, will help bring us a step closer to vital industrial decarbonisation and beyond.“It’s increasingly important to get the technological solutions we need to reduce emissions right first time, so carrying out these detailed and industry-supported projects at the University of Sheffield Energy Institute means we can test, scale and ultimately implement these alternative solutions as efficiently as possible.”
Hydrogen – a big part to play
Chris Lovatt, chief operating officer for UK Solutions at E.ON, said that hydrogen will play a significant role in our energy future, mainly powering energy-intensive industries and long-distance transport. He believes it sits alongside the drive for heat pumps meeting domestic heating needs and a greater role for district energy schemes in urban areas: “The first stages of our trial show the technology works and can support the industry’s needs for alternative fuels as well as Sheffield’s wider sustainability ambitions.
“We know there are challenges to overcome before this becomes a viable solution for industry, but the success so far has been rewarded by further funding from the Government to explore the potential of green hydrogen as a solution for Sheffield’s world-renowned steelmakers.”
Rob Ireson, innovation and partnerships manager at Glass Futures, added: “We are excited to begin the next phase of this project to evaluate the performance of hydrogen and hydrogen-natural gas blends in steel manufacturing furnaces. Using data carried out in our Combustion Test Bed furnace in the first phase of research, which also formed the basis of the modelling carried out by the University of Sheffield, we can begin to apply the method for simulation and testing of hydrogen firing to furnaces at an industrial scale, to verify hydrogen’s effectiveness.”
Green hydrogen is produced by splitting water into both hydrogen and oxygen through a process called electrolysis. Using electricity from renewable sources means it is seen as the cleanest option for industrial uses.