
Our thought leadership article where we hear insights on the transition from voices both inside and outside of our sector. Here, from our May issue, Kevin O’Neil, senior business leader for renewable fuels at Honeywell, considers feedstocks for SAF.
With aviation one of the hardest to decarbonise sectors, Kevin talks us through the feedstocks that can fill the current and future production gap and explains how Honeywell UOP is developing conversion technologies to enable them to deliver at scale.
All human progress starts with someone suggesting that “there has to be a better way.” Today, this thought is being considered around the world as we confront the challenges of the energy transition. Honeywell UOP, a company with a rich history of developing and delivering technology to the petroleum refining, gas processing and petrochemical production industries, is applying its expertise in innovation to the development of a diversified technology portfolio for sustainable aviation fuels.
In any consideration of decarbonisation goals, the main fuels that come under scrutiny are diesel, jet and petrol (gasoline). With electrification largely viewed as the answer to the decarbonisation of transport, especially light transport, a lot of technology is also already in development to support the decarbonisation of heavy transport through electrification combined with other routes.
The bigger challenge
Decarbonisation of aviation remains the bigger challenge, with the industry seeing sustainable aviation fuel (SAF) as the only real near-term solution.
When the technologies behind renewable process units were first commercialised, they were mainly commissioned for production of low carbon road diesel rather than aviation fuel. This focus shifted around the start of the pandemic, with a rapidly growing awareness of the massive increase in SAF production volumes needed to decarbonise aviation. In September 2021, Joe Biden announced the SAF Grand Challenge in a bid to find the solutions to scale up US production to 3 billion gallons by 2030. With production at that time only around a couple of million gallons per year this represented a commitment to increasing capacity by several orders of magnitude.
European goals are comparable, accelerating further after 2030 to targeted annual production of 10s of billions of gallons.
SAF is not like crude oil, with millions of barrels a day readily available for extraction, meaning that multiple pathways will be required to achieve this level of production. The current feedstocks, primarily fats, oils and greases (fogs), are relatively limited, so a key focus area for Honeywell is to develop, launch and commercialise new technical pathways to enable the use of additional feedstocks in the production of these renewable fuels. Kevin talks us through these developments.
As a company used to developing technology solutions for the oil and gas sector this is something that is a very natural fit for us. We already have the pilot plants, research people and infrastructure to be able to develop these new technologies and these are the main feedstocks we believe have the potential to plug the production gap.
Ethanol
We see ethanol as a really promising feedstock that is already produced in large quantities in the US as a gasoline blend stock to meet the requirements of the renewable fuel standard.
With increasing transport electrification, ethanol producers are seeking alternative uses. Converted to jet fuel relatively inexpensively, US ethanol is largely high carbon intensity corn-based production but with US SAF incentives requiring at least a 50% reduction in carbon intensity relative to fossil jet, this needs to be reduced. Plenty of activity around solutions such as carbon capture on the fermentation process will, ultimately, enable high volumes of low carbon intensity ethanol to be produced making this source of biogenic emissions a feedstock pathway to significantly expanding available quantities of high quality SAF.
It is one of the main routes Honeywell is working on and we launched our ethanol to jet technology last October to significant interest, not only in the US, but also in Asia and worldwide.
But, while ethanol to jet will make a highly significant contribution to increasing SAF availability, there is no single silver bullet to achieve targeted quantities, with a range of solutions needed.
Biomass
Another potentially significant contributor to achieving SAF production goals is woody and agricultural biomass, by-products from forestry and agriculture that are readily available in large quantities. The challenge in making drop-in fuels from this material is that their conversion is not simple, but the technology exists to do it. Combined with efficient collection mechanisms of these waste materials, we see woody and agricultural biomass as potentially significant SAF feedstocks.
CO2
Carbon dioxide (CO2) is also gaining traction as a major feedstock, especially in Europe where its use is driven by a number of incentives and mandates around the use of e-fuels. Developing new technology to combine CO2, captured from either the atmosphere or industrial flue gases, with green hydrogen to produce SAF is another area that we’re very active in.
While producing SAF from CO2 has its challenges, there is potential for significant production cost-reduction that we expect to make this a competitive option for producing SAF.
Repurposing
An important focus for us is developing ways to repurpose existing refinery equipment to produce renewables, enabling our customers to make rapid transition progress.
Many of the emerging SAF production technologies, such as CO2 capture, involve new builds, but can often still be integrated into an existing facility reusing some of the equipment. With decades of engineering expertise, we can evaluate how well existing equipment can be used for a different purpose than it was originally designed for.
Those currently producing fossil fuel have the infrastructure, the capital and the know-how to deliver decarbonisation solutions the quickest and Honeywell is working with these energy producers to achieve a sustainable future.
It’s how we’ve always cooperated with the industry, developing new technologies that those in the industry can use to convert whatever feedstock they have into a valuable product. With the major focus now on the need to decarbonise, our input is about enabling those major players to continue to have a part to play as the sector transitions.
We have significant in-house capability, but we also work with customers and organisations, such as universities, as appropriate.
There’s a host of other feedstock options under consideration – polyester clothing, tyres and municipal solid waste get a lot of attention – they’re not going to be easy to scale but part of my job is to prioritise and say: “Okay, these are the ones we’re focusing on, but there are others with smaller prospects we still don’t want to ignore”, because there are many solutions that may have a role to play.
Municipal solid waste, tyre pyrolysis – they may not be the easiest routes, but we’re trying to figure out ways to make them economic and competitive with other pathways to renewable production.
The clarity challenge
Lack of clarity will always be a challenge in the development of new feedstocks and technologies. Legislative certainty and the right regulatory environment in emerging markets will deliver greater levels of investment. Whereas, if rules may potentially change in the shorter term, the lack of certainty makes it more challenging to secure investment to progress potential solutions.
Feedstock solutions for renewable fuel production will also vary geographically depending on both demand, historic industry and availability of raw materials. We see a fair amount of concern in Europe over the repurposing of vegetable oils and we don’t see ethanol as significant because of the perceived repurposing of a food crop to fuels as well as the lack of infrastructure, but the development of biomass as a renewable fuel feedstock is more advanced in Europe than the US.
The feedstocks we’ve considered are the ones for which the technologies are ready to be deployed today. There will, ultimately, be other solutions emerging that that we haven’t even considered yet, and we are studying others. We’ve done a lot of fundamental research and we have people looking at other routes that we see as potentially very interesting, but they need time in development, before they can be launched and scaled up.
Right now, the industry is pretty strong. In a rapid transition, there is a lot of new development and new technology being talked about and launched, making it an exciting time for our sector. Most companies emerging from the pandemic saw a downturn and a resultant headcount reduction but now I wish we had more people here because there’s so much going on!
In terms of recruitment, there’s a very positive vibe over the energy transition and, as a company committed to this and making a significant investment in the development of future fuels, I believe we attract a lot of good talent.
Achievable targets
Given current production levels, we believe that the 2050 targets are achievable. The feeds are available, and the technology is ready – it just needs to be deployed now to start us on the journey to reach those levels.
Other mechanisms, such as effective feedstock collection, will also increase the efficiency of production. The emerging market for used cooking oil sees the restaurant sector, having previously viewed its disposal as an inconvenience, now storing it under lock and key as well as the launch of companies specialising in its collection as it becomes an increasing valuable commodity.
The right support mechanisms will need to continue to emerge to enable a broader array of feedstocks, whereas, for ethanol, that infrastructure already exists with established US ethanol capacity in the US currently exceeding 17 billion gallons.
Ethanol will become increasingly available as a feedstock for SAF as electrification reduces its demand as a gasoline blend for transport, but the question is, how long is that going to take?
In the long term, it seems inevitable that electrification will ultimately take over but, even with the ban on sales of fossil fuel powered cars after 2030, it’s still going to be a slow decline. Liquid fuel demand for transport continues to grow and, in many emerging markets, won’t be plateauing or declining in the near future. This also means a continuing demand for ethanol in meeting road transport obligations but the ‘blend wall’ means that ethanol is already a little bit long leaving producers putting plans in place to repurpose their production. With the inevitable longer-term decline in both ethanol demand and price, we are already talking to producers who are keen to be the first to enter the SAF production market. Demand for SAF is, effectively, infinite compared to supply but the cost of production is inherently more expensive than for fossil jet fuel whether it is made from fats, oils and greases, ethanol or other feedstocks.
Governments are currently helping to foot that bill using incentives to protect the consumer from the cost differential. This is where companies like Honeywell have a role to play, improving emerging technologies to increase efficiencies and reduce costs. A substantial element of the cost of production lies in the feedstocks themselves along with processing costs, as well as building the plants and amortizing those costs. But there are also costs related to plant operation and we focus a lot of our attention on minimising these – though evolved technology, better catalysts and improved process – to ultimately drive the cost down and make the fuels more competitive as they scale. It’s what we have done for generations in the oil and gas sectors.
Having only recently launched our ethanol to jet solution we’re already looking at ‘gen two’. How are we going to deliver better yields and lower energy costs to bring the cost of these pathways to SAP down and achieve parity with fossil jet production.
It is going to be challenging and it’s going to take some time, but we do see that ultimately, as a reasonable goal.
Kevin M. O’Neil is the Senior Business Leader, Renewable Fuels, for Honeywell UOP’s Sustainable Technology Solutions business unit, leading Honeywell UOP’s licensing business for technologies to produce renewable diesel and sustainable aviation fuel. With more than 34 years at Honeywell UOP, all working with oil and gas technologies, he has held positions in technical service, business management, and sales, including most recently as Senior Business Leader of Honeywell UOP’s Aromatics licensing business. He has a bachelor’s degree in chemical engineering from the University of Illinois and an MBA from the University of Chicago.
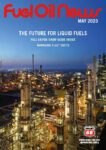